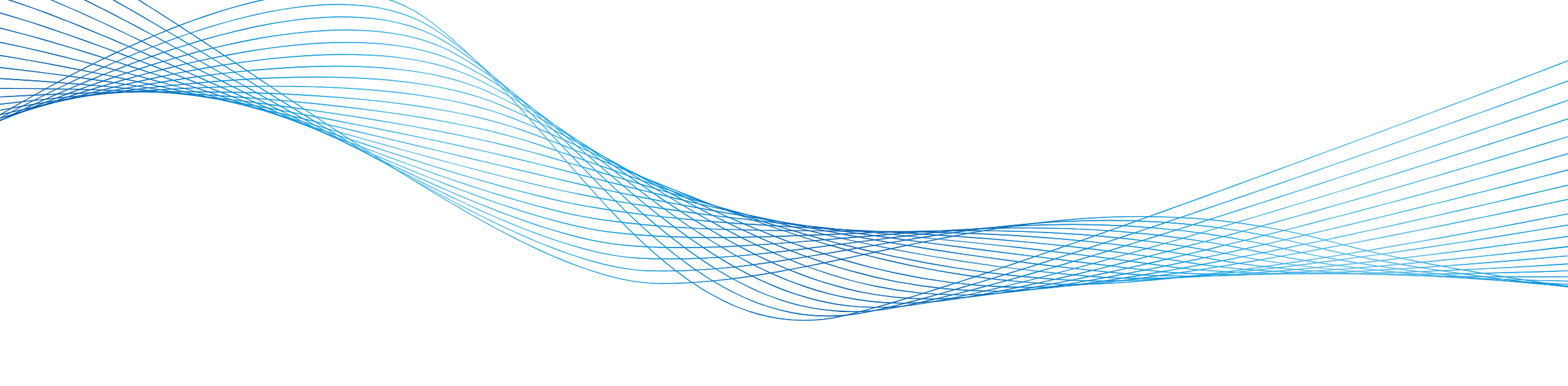
News
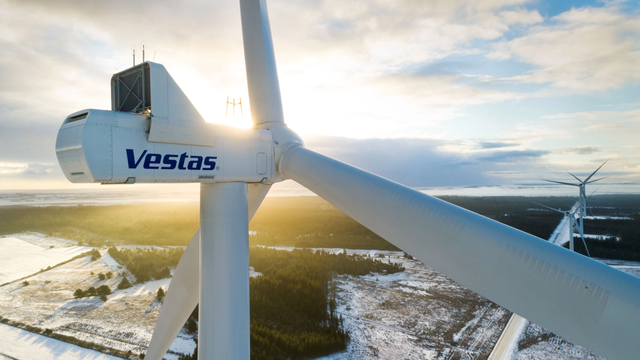
Supporting Global Wind Power Generation with Power Semiconductors
Amid the decarbonization movement, renewable energy such as wind and solar power generation is becoming increasingly widespread in recent years. The voltage and frequency of wind power generation output can vary depending on the strength of the wind and other factors. Therefore, in Japan, it is necessary to convert the frequency to 50 Hz in the east and 60 Hz in the west. This process is handled by power semiconductors in power converters. Fuji Electric has succeeded in creating power semiconductors for these renewable energy generation systems that are smaller in size and higher in efficiency. Our power semiconductors support Vestas, which boasts the world’s top market share in the design, manufacture, and sale of wind turbines.
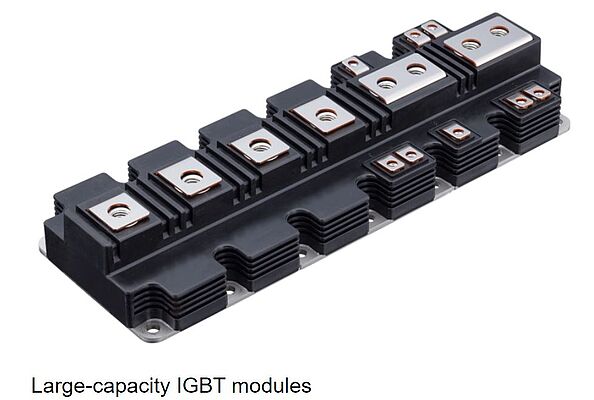
Supporting the world’s leading wind turbine manufacturers
In northern Denmark, you can see lines of huge turbines that generate wind power. These turbines use large-capacity IGBT modules, which are one of Fuji Electric’s power semiconductors. Yusuke Sekino of the development department comments on the role of power semiconductors in wind power generation, saying, “In wind power generation, the force of the wind spins the blades, which in turn rotates the generator to generate electricity. To feed this electricity into transmission lines, it is necessary to change the voltage and frequency. This process of power conversion is where our power semiconductors shine. In fact, Fuji Electric’s power semiconductors meet the high expectations of Vestas, the world’s number-one manufacturer of wind turbines.”
Developed a system to meet supply needs in just one year
It was in 2017 that the Denmark-based Vestas approached us about supplying a new power semiconductor. Vestas’s biggest challenge in selecting a vendor was the ability to provide a stable supply of new devices. To meet this need, Fuji Electric established a cross-functional team to cover sales, marketing, development, procurement, quality control, and more. With thorough cooperation among departments and repeated discussions with parts suppliers, we achieved the successful vertical start-up of a development system to accomplish everything from planning to mass production testing in a short period of time, and we committed to supplying products to Vestas, thereby earning their trust. Looking back, Katsuhiko Takagi, a sales representative who served as the project leader, says, “Wind turbines are a rare sight here in Japan, but in Europe, national-level projects are starting up one after another, and demand is growing even higher. That is why our major premise was to supply many products and to do so stably. Establishing whole process up to mass production usually takes nearly three years, but we were able to develop it in just one year. This was because everyone across departments took on the challenge of introducing the new technology involved in the launch the product. I am so proud of the people who worked on this project.”
Pushing Fuji Electric’s quality to the limit with no compromises
Another challenge in landing the order from Vestas was improving the product characteristics. Through a process of repeated trial and error, the development department successfully reduced power loss by utilizing cutting-edge technology and applied a substrate with high heat dissipation to successfully improve the output power of the IGBT module.
“To increase the output power, it needs to reduce the resistance of the semiconductor by making the chip thinner. However, making the chip thinner causes the withstand voltage to decrease, which makes the product more prone to voltage-related breakdowns. These two requirements seemed to be mutually exclusive, but we moved forward with ongoing and thorough verification. This project had the potential to significantly influence the future of the semiconductor business. The project members also approached development with strong conviction and motivation.”
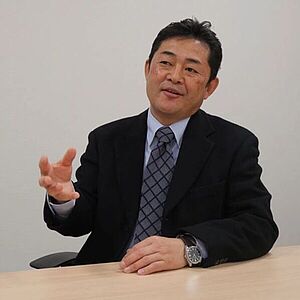
Respond to the highest compliment with further challenge
Once we had achieved solid quality and a stable supply, Fuji Electric was able to deliver power semiconductors without delay for an important project that Vestas was promoting. In recognition of this achievement, we were awarded additional supply contracts.
“When the Vestas management members came to Japan after the project was complete, they said, ‘You are a hero in Vestas!’ That was the biggest sense of accomplishment I’ve ever felt,” says Takagi. “The world is beginning to make major moves toward decarbonization. I’m proud to be able to contribute to this challenge with our technology, and I feel excited about the challenges ahead.”
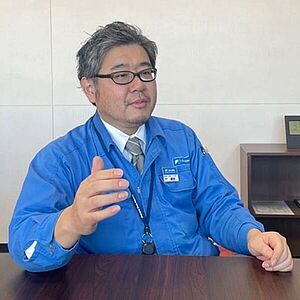
“Power semiconductors have great potential,” says Sekino. “In addition to contributing to renewable energy like in this project, as well as to railways, automobiles, and other forms of mobility, they are also expected to be very useful in the challenge of contributing to next-generation fuels, such as hydrogen generation using electricity. Further, the performance of power semiconductors themselves can be dramatically improved by the use of a new material called SiC (silicon carbide). For us engineers, I think it is a great pleasure to continue the challenge of finding more potential.”
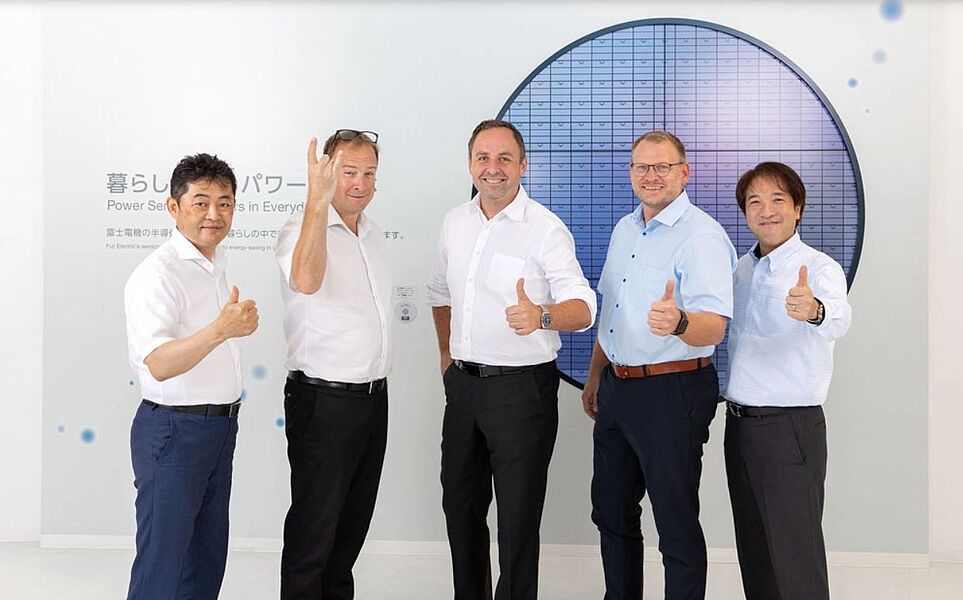
From left: Katsuhiko Takagi, Sales Dept. I ,Sales Division, Semiconductors Business Group;
Dr. Philip Carne Kjaer and Jacob Gottsche, Vestas Wind Systems A/S;
Christian koch, FEE; and Masayuki Tsuda, Sales Dept.